Change brewing
A $42 million revamp of four former brewery buildings is nearing completion after an extremely tight nine-month construction period.
On a rare 5.2 hectare site on Khyber Pass in Newmarket, the University of Auckland is developing a post graduate engineering research precinct that will bring together students and staff who are currently scattered across the university’s city and Tamaki campuses, along with equipment that is housed in various leased spaces around Auckland. The facility will be home to an array of specialised equipment including a 45-metre, 50-tonne flume and a wind tunnel, and will provide more integrated spaces from which to showcase research programmes.
Upon first contemplation, acquiring the former Lion Breweries site and undertaking a massive refurbishment of four existing buildings to the tune of $42 million doesn’t seem like the obvious choice, but architects Chris Jack and Tristram Collett of Jasmax saw the potential of the warehouse-style buildings that formerly housed brewing and bottling facilities. During the due diligence phase the decision was made, by University of Auckland Property Services in conjunction with consultants Jasmax and BGT Structures, to reuse the buildings.
“There were a number of high volume spaces within robust structural buildings that Lion used as processing facilities,” Collett says. “Essentially this project is a sustainable overlay; a commitment to reuse. The challenge was making it into a research precinct, and to feel like home for the people who will work there.” The large site drops down about 15 metres between the top of the site at Park Road and the Newmarket end; the buildings were originally terraced over four levels, but this project has seen the addition of a further two levels (and a central ‘link’ building that will become the main entry to the site).
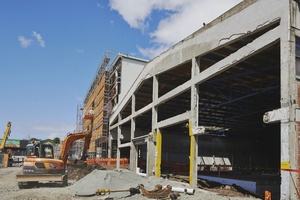
Hawkins Construction was awarded the contract to revamp the four buildings in mid-2013 and started on site in September that year. The project is scheduled for completion in July 2014, in time for students to occupy the building in the second half of the academic year. This tight timeframe essentially requires more than
$1 million of work to be undertaken every week.
The complex contract incorporates, along with the recladding of the four buildings (901, 902, 903 and 904), construction of the link building, seismic strengthening, fit outs, a package of demolition, and the ring main services for the entire site (the Hawkins part of the project covers just over half of the 5.2 hectare area). Hawkins project manager Craig Treloar says the incredibly tight construction schedule is one of the main challenges he and his team are facing.
When Progressive Building visited the site in late January about 220 tradespeople were on site. “Because it is essentially a renovation, the areas are all being run concurrently so you haven’t got the flow you normally would with a new building,” Treloar says.
However, the challenges are aplenty. Each of the buildings required a different level of seismic strengthening (two of the buildings, 902 and 903, are connected but are seismically separate). Building 901 required a significant amount of attention; the pitch of the roof was raised, it was re-clad and a mezzanine level for offices was added. “To bring it up to code we had to put new piles in. The new piles are connected to the existing shear walls, which were fibre wrapped to increase their strength.”
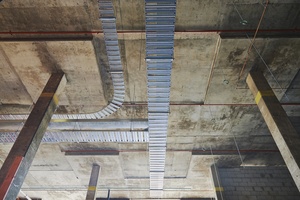
The new piles were drilled down to about 20 metres; this was achieved by utilising a piling rig inside the building in a space just 6.4 metres high. “The existing roof had a very shallow pitch so it was raised to seven degrees. Large structural steel sections were bolted together on the ground and lifted into place with a mobile crane.”
This building will house a number of specialist laboratories, in which gases including argon, hydrogen, LPG, methane, nitrogen and oxygen will be required. Treloar says the services required in this building are of similar capacity to what you might expect in a hospital. “The interior is very rustic and exposed, which is a challenge in itself because added to the complexity of the services required, having them exposed means they have to be absolutely perfect.”
In building 904 the drainage was upgraded to suit the new space so a whole new system was installed. “We also had to cut out under each column to strengthen the foundations. New foundation beams were required, and we are adding structural steel to each of the columns to strengthen the walls.” This building will be home to the fluids laboratory and will house the university’s 45-metre, 50-tonne flume, which will sit on a specially designed foundation and circulate water from a below-ground reservoir.
“Excavation for the flume’s reservoir was approximately four metres deep and covered 32x12 metres inside the existing building. The amount of groundwater inflows that we had to control and constantly pump out was a challenge.” In order to mitigate the issues with water during construction, Treloar says water is pumped out of the reservoir continuously, which is an ongoing challenge.
Architect Chris Jack says the site was originally chosen for a brewery precisely because of these natural springs running beneath it. All the buildings are being re-clad with a combination of vertical metal claddings, Danpalon (translucent polycarbonate panels), and plastered masonry. While the focus is on the interior spaces, the cluster of buildings was lacking a main entry, something the architects spent some time achieving.
“There was no obvious sense of arrival or entry, so the new link building will achieve that. Pedestrian access will start from Park Road, and lead towards the link building where people will be dispersed to different areas. An internal corridor was already there - that has became a natural device to circulate people within the buildings. This focus was a main one - on internal pedestrian routes,” Jack says.
While some of the spaces didn’t lend themselves freely to conversion for use by the university, others did. In building 903 one of the levels, formerly used as a bottling line, had a significantly lower ceiling height than the other levels, lending itself to office space. “Two skylights were introduced in this building, which allowed us to bring light deep into the floor plate and into this middle office level.”
Despite the renovation of these buildings providing a relatively temporary solution for the university, the finished project will provide approximately 20,000m 2 of high quality floor space. The Hawkins part of the redevelopment is just phase one of the university’s vision for the precinct - something that is likely to develop significantly over the coming years. Phase one covers just over half the site, and in December 2013 Scarbro Construction was contracted to construct a new building, 906, at the Newmarket end of the site that will provide a facility for civil engineering research and incorporate a nine metre strong wall, one of the largest seismic testing walls in Australasia.
“The Newmarket Campus will join the city and Grafton campuses to create an integrated campus cluster, supporting long term growth enabling the university to deliver to Auckland and New Zealand the full benefits of a multi-disciplinary, world-ranked research university,” vice-chancellor, professor Stuart McCutcheon says. “Over time we anticipate relocating activities from the Tamaki and Epsom campuses to the City/Grafton/Newmarket location. The timeframe over which this relocation occurs is yet to be determined, but ultimately this is expected to result in a significant reduction in our total landholdings.”
University of Auckland Property Services will manage the completed buildings on an ongoing basis.