Behind the Object: Te Hau-Ora, The Breath of Life
In October 2019, Jasmax launched a new brand identity with, among other things, biculturalism at its core. Part of that new identity was the creation of Te Hau-Ora, which takes the form of a 3D-printed kōauau (inspired by the traditional Māori flute played in spiritual ceremonies). The company says, “Created as a taonga to honour current employees and welcome new employees into the practice, Te Hau-Ora recognises the importance of belonging to a place of long connection to our land and its people, and it is designed to be passed on from one hand to another in a ceremonial exchange.”
Jasmax’s marketing communications advisor Heidi North explains more about this new tradition within the firm and sits down with some of the team who designed the kōauau to learn more about the process of creating the unique item.
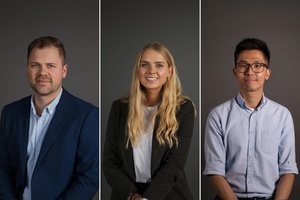
Here, Te Hau-Ora’s designers – associate principal and digital design lead, Tim Stephens, senior associate and architectural designer, Zee Shake Lee, and graduate designer, Sophia Cameron – discuss the design.
Heidi North (HN): What lead you to the creation of Te Hau-Ora?
Zee Shake Lee (ZSL): The story of Te Hau-Ora began with a block of purple heart timber salvaged from the Queens Wharf redevelopment, gifted to Jasmax by Panuku. Jasmax has a long association with Queens Wharf, having led the redevelopment of the wharf and its opening up to the public in 2011, and the redevelopment of Shed 10.
HN: Why was it important to use a piece of a past Jasmax project?
ZSL: The material carries a history and story of its own and embeds the idea of legacy into the project, which was an important component for us. This project is very much about connections, between the human agency and the object we design, the physical and the intangible, people and place, form and function, and the present and the past.
Tim Stephens (TS): Before we were gifted the timber, we had already started experimenting with creating a taonga, but we didn’t know exactly yet what material it would be made from or what form it would take.
HN: When did the idea of 3D printing come into it?
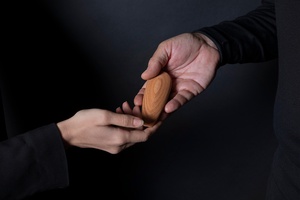
Sophia Cameron (SC): I’ve worked with 3D printing from waste materials, including timber, before, and with Tim’s expertise in digital innovation we were interested in creating something that pushed the boundaries in that space. When we were gifted this incredible piece of Jasmax history, we started to explore opportunities.
HN: The design process was very collaborative wasn’t it? How did you come to the final idea?
TS: When we started developing the idea of creating a Jasmax taonga, we worked in conjunction with Karl Johnstone from Haumi, and master carver and Māori artist, James Rickard. We initially were designing something simpler, an object, and exploring the materiality of how you interacted with the object, and the giving of life through touch – much like how a pounamu is polished through the wearer. Then Karl introduced us to the idea of the kōauau and we were off.
SC: It resonated with what we wanted to achieve, the idea of breath signifying the life and energy we breathe into our environments and designed spaces, as well as the breath we share with each other. It’s a very personal gift to be worn and treasured, but it’s also something that can be used internally for playing at special ceremonies or celebrations
HN: A 3D printed version is quite different to a traditional kōauau, how did you decide to go in this direction?
TS: We still weren’t sure we were going to at this stage. We were going through a considerate research and design process, figuring out how to make this playable. Working with James, we would 3D print something, James would carve it and we would then explore the design in parametric computer software.
ZSL: There was this wonderful cross over between analogue and digital process, which carried on throughout the project.
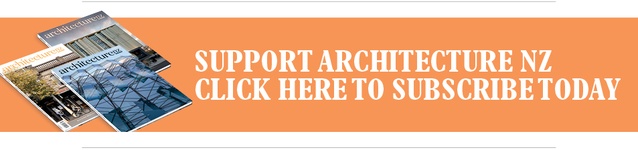
HN: When did the idea of carving it digitally come into it?
SC: Not only is 3D printing resource efficient through additive manufacturing, there is also an incredible amount of design detail – patterns and digital textures – we can achieve using digital carving techniques. We recognised this early on in the process and thought that it fitted the overall story we wanted to tell. 3D printing with reclaimed timber is fresh playing ground, so this was new, and exciting, for all of us.
HN: The form is also quite different from a traditional kōauau. Tell us about how it came about.
ZSL: Te Hau-Ora is a careful reinterpretation of a traditional kōauau, we were deliberately trying not to recreate it, but we were keen to incorporate the values of a traditional kōauau but make it contemporary – the blend of tikanga and technology.
SC: The form references the curvature of the human body and our New Zealand landforms, it is a collision of the two – it represents our people, the people we design for, the environments we design in and the buildings we create. The texture takes inspiration from nature and Ta moko – a traditional tattooing method where lines follow the body’s form and move with its curvature. It connects to the ideas of movement and growth and is designed to fit seamlessly into the palm of the hand and to be worn close to the chest to have that connection to people’s hearts.
HN: Did making a playable flute come with challenges?
TS: Absolutely! It was seriously challenging – we had to work out how a flute makes its sound, and then make it into a form. That’s when it got really complex. We knew why they were made, but we had to discover the how. James took us through the traditional ways they were made, and the different forms and materials. It was an incredible process.
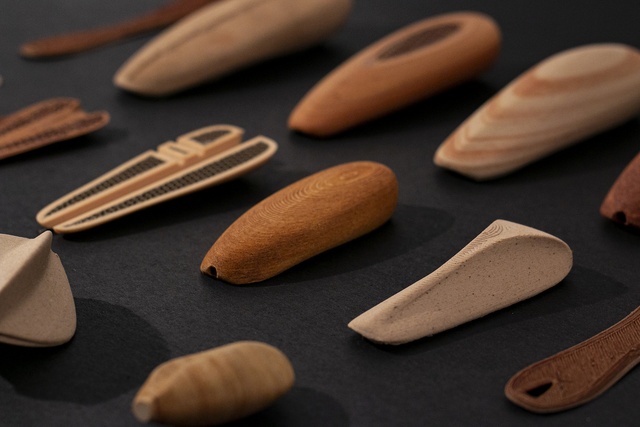
HN: How did you get from a block of salvaged wood to a playable kōauau?
TS: It’s quite a process! First of all, we realised that we needed to get the wood fine enough to prototype with scientists at Scion. As this is all so new, we knew we had a lot of testing to do before we could get to the final product. And that’s when we realised there wasn’t really machinery readily available to grind the wood fine enough.
Well, there was me in the garage for hours on end, sitting on one of the kids stools, with a heavy-duty belt sander hooked up to vacuum cleaner trying to sand it down and generate enough powder for the scientists to start testing it for us. There is still dust from the purple heart timber all over the garage. That was an intense moment – but we all believed it in, and we were going to do anything to make it happen
SC: From here, we figured out a way for the powder to be produced in a wood workshop, and after we ground enough raw timber down to wood flour, we prototyped and researched it in conjunction with Scion to create a custom-made, biodegradable, 3D-printable timber filament. This involved combining the wood flour with a plant-based binder made from sugar and corn starch, extruding it into3D printing filament, hand-dying with natural wood stains, digitally crafting it and then finally it gets 3D printed.
HN: How did the hand-dying process work to get the colour you wanted?
SC: We wanted to retain an element of hand craft in the process, so the 3D printing filament was personally hand dyed prior to it being 3D printed.
TS: There were many days our hands were stained at work.
SC: We had to experiment again to get the colour right. The colour of the natural material is quite strong, but it lightens when combined with the biobased binder, so we wanted to stain it to return it to its natural colour. The filament is only stained on the outside, but then it re-melts when it goes through the 3D printer and that deposits the filament in a really interesting way. As each piece is 3D printed, it takes on a new colour of its own.
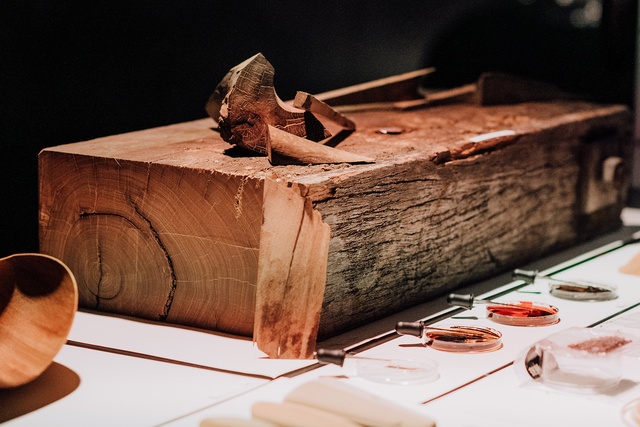
HN: So it’s impossible to replicate these, despite them being 3D printed?
SC: That’s right. Each kōauau is unique because of the hand staining. Even the texture is almost like a fingerprint, every time it prints that surface the colorations change and, despite being 3D printed, it starts to look like a wood grain.
HN: Again there is this cross over between digital and analogue process isn’t there?
ZSL: Yes, we didn’t carve it with hands, but we included some hand making elements to the process, which gives each one nuance that makes it unique.
HN: How long does each kōauau one take to print?
SC: It takes about three and half hours to print each piece.
HN: How have they been received?
SC: Some of the feedback I’ve had from people is that they do feel a deep sense of belonging. Because while the project celebrates the collective values of Jasmax as a whole, they are also gifts that celebrate each individual person.
TS: It’s been a powerful process to watch. The whole project was initiated by the leadership team after taking inspiration from Ngāi Tahu, who gift their staff pounamu when they start with them. This is our offering in that space, and the project was kept a surprise from the practice until the new design direction launch. It was amazing how positive everyone has been about them.
ZSL: And people do wear them on a day to day basis, for example when they go to client meetings. And you hear it played in the office quite often! There’s one particular person at work who you can hear practicing playing it around 5pm each day. It’s wonderful to see and hear them being used, and loved, by people.
See more from the Behind the Object series here.