Flatpack future
The $10 million remediation of a retirement complex in Papamoa is challenging the status quo, providing an alternative way of dealing with leaky buildings.
In a factory tucked away in rural Matamata, eight people are working full time to construct fully compliant, flatpack wall panels, which are trucked to site and quickly and easily installed, as part of an innovative multi-million dollar remediation of Lend Lease’s Ocean Shores Retirement Village.
Extensive damage was evident at the property, which incorporates 84 units in two three-level buildings, Block A and Block B, a single-storey central building housing the reception and common areas, and a pool building, which was demolished and will be rebuilt as part of the project.
Upon completion, the project will see the three buildings brought entirely up to current Building Code standards, as opposed to the general practice of replacing only targeted areas of a leaky building, and as such, only bringing those replaced areas up to standard. Although more timber is replaced overall, the process of entirely replacing the majority of the buildings’ facades is far more efficient than the traditional targeted approach.
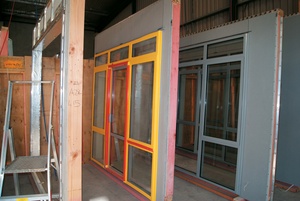
Throw off-site flatpack construction into the mix and you have an incredibly efficient process, cutting down what would normally be a 24-month project to just 10 months. “The productivity increases are huge,” Stanley Group managing director Kevin Stanley said. “Because it is a full timber re-frame, we are upgrading the whole building to meet current Building Code standards, which means the client is getting surety.”
Stanley Group began dabbling in this sort of approach to building more than a decade ago when they started working with modular construction. “The Chateau Tongariro was one of our first modular projects,” Mr Stanley said. “We worked with Carters on that project. Since then we have evolved. Carters shut down their business and we took over their assets and moved the operations down to Matamata.” The Chateau project involved the addition of 40 extra rooms to the heritage-protected building. Modules were constructed off-site and lifted into place by crane.
Despite the advantages of modular construction, there are also disadvantages that are not evident in flatpack construction. “If you are building a module, the biggest problem you have is transporting that module to site. If you manufacture a wall panel, you don’t have to transport all that air, and that issue is removed entirely,” he said. “There is a big place for modular, but the real opportunities are out there in flatpack construction.”
When Progressive Building visited Stanley Group’s Matamata factory in late May, it was a hive of activity. In four areas, wall panels were at different stages of completion. Manufacturing manager Sean Wood said the 300kg flatpack panels were only ever moved twice, once from horizontal to vertical, and then mechanically loaded onto a truck for delivery to site.
“Each panel is built in four stages; construction of the timber frame, then application of the RAB board and aluminium, including the Protecto flashing tape. The panel is then moved to a vertical position and the joinery and windows are installed, followed by the cladding,” Mr Wood said. A council inspector signs off each panel before it leaves the factory.
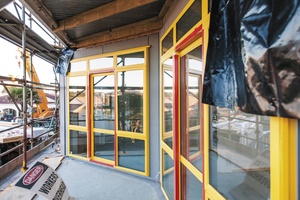
Mr Stanley said the benefits of this style of construction extended to health and safety, by allowing, for example, the 85kg windows to be moved by suction cups instead of what would be a four-man job on site. “We are manufacturing here what they will need on site in a week’s time. We did a complete survey of the site so we knew exactly how big each wall panel needed to be. BIM modelling is absolutely critical. Everything has to be designed in 3D to make sure it will actually fit together. With this type of construction, the tolerance is lowered to one or two millimetres. The key is to start with the BIM modelling, design and plan the hell out of it, and when you have planned it, plan it all again.”
The project, which started in March 2013, is on track for staged completion from August. Site manager Jason Hill said around 60 staff were on site on an average day. “The buildings are essentially going to look like concrete carparks. Everything on the east and west facades is coming off completely. On the ends of the buildings, the north and south facades, targeted work will be done as opposed to a complete reframe,” Mr Hill said.
“But because it is still based on a cavity system, the whole building is brought up to code. So we will remove the cladding, windows, all the interior linings from Level 3 of the north and south facades. Then the framing that is to remain will be brought up to code with additional fixings and structural elements or more timber framing added if required.”
Two months into the project, work was well underway on Block A, with work on half the building starting from the ground up, and on the other half from the roof down. All 84 apartments have balconies, which are being completely upgraded as part of the project.
“A new system is applied to the front of the balcony, along with a new glass balustrade and a new membrane system to the top of the balcony. A new sill, which is a compressed liquid concrete, is put in place, and a new bottom plate. The membrane from the balcony then gets extended up and over that bottom plate to the interior face of the new frame. The flat-pack panel is designed to fit in conjunction with the new sill detail we put in.”
Although nothing is changed structurally, significant work is required on site before the flatpack panels are installed. This includes levelling of the whole building, and the installation of the new bottom plates, sill and membranes. “Both buildings are not level. Block A is between zero and 40mm, and Block B ranges between zero and 75mm. These are huge inconsistencies that we dealt with by installing new bottom plates,” Mr Hill said.
Although the panels are part of a compliant, standardised building system, they can be slightly altered at the manufacturing
stage to fit specific requirements, making each one a bespoke panel. As well as flatpack construction, removing the need to wrap the building was a crucial part of ensuring the build was completed quickly and efficiently.
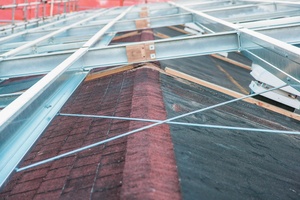
From the rooftop of Block A, another remediation project down the road is glaringly obvious. The whole building is wrapped, in stark contrast to the Ocean Shores site. “We decided to use the old roof as temporary waterproofing while we are putting the new one on,” Mr Stanley said. “We designed the project specifically to use the existing roof in this way. If you fully enclose the roof it slows down the process. By working this way we are able to manufacture and bring in big items. If we had a tent over the site that wouldn’t be possible because we wouldn’t be able to get a crane in. The whole premise of this job is speed. Being able to put the new roof over the old one has been essential for this.”
Mr Hill said penetrations were cut through the old roof, and structural steel columns were installed from Level 3 floor level up through the existing roof structure. “In between the columns there is a 300 x 90mm LVL. The existing roof is bolted right through the LVL so when the exterior wall below is removed the roof section stays in place and does not collapse,” he said. The roof panels were divided into sections and constructed on the ground. The sections are then craned into place and installed.
Because the Australian arm of Lend Lease is the client, rigorous health and safety measures were required to be implemented on site to bring procedures that would normally be undertaken in New Zealand up to Global Minimum Requirements. “It is a real culture change for New Zealanders. There’s a lot of guys here who are not used to doing things this way,” Mr Stanley said. “But we had really good buy-in. We involved some of the subcontractors when we were developing the process so they got to understand it and have input.”
The raised bar required, in addition to regular tool-box meetings, daily site safety meetings, followed by a co-ordination meeting for supervisors. It also meant the level of incident reporting shot skywards, but Mr Stanley said this was not a bad thing in itself. “We report more incidents on a job like this because people are more aware,” he said. “Part of the culture of change is encouraging reporting. Although our reports have gone up ten-fold, it is a good thing because it prevents incidents turning into accidents. If you can report an incident you can prevent it happening again.”