Novotel Hobson hotel
With a design that accounts for a protected tree, the Novotel Hobson hotel in New Plymouth is more than the sum of its parts.
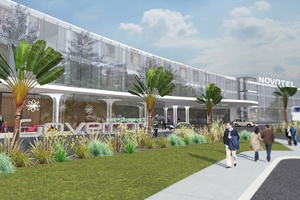
Sleek, stylish and fit for purpose, the new Novotel Hobson Hotel in New Plymouth will be “a welcome addition to the city and support the more discerning business traveller,” says architect Murali Bhaskar of Boon Goldsmith Bhaskar Brebner Team Architects. The hotel, which is currently under construction (30 percent into the build at interview time), flanks the gateway to the city on State Highway Three. The artist’s impression shows a long, concave building with a 100m double-glazed curtain wall. The building is approximately 120m long and 17m wide with 100 accommodation rooms that include studios, executive suites and apartments, a restaurant, bar and outdoor dining facilities, conference facilities, meeting rooms, pools and spa.
The feasibility study done by a hotel consultant gave the architects excellent design and budgetary parameters.
“The building fell out of that detail really,” Bhaskar says. “It’s hugely important for architects to know the funding model works so you are designing a facility you know will operate successfully at reasonable costs and will therefore recoup your capital outlay, so the development becomes sustainable.”
The contemporary style of the hotel balances the aesthetic with budget, aiming for “something that is timeless, clean-lined and simple with not too many material palettes around the building. The glass façade will be a prominent feature and will either reflect or be transparent depending on the time of day and level of sunshine,” Bhaskar says. “The hotel will have an attractive interior and be warm and welcoming. It also has to tick a few brand standard boxes for Novotel.”
The team approach between consultants and contractor has proved highly successful but with demands on both sides, says Dean Hope, project manager for Foster Construction.
“That is the nature of the building industry at present. All three parties have a very open mind and bring to the table both experience and helpful solutions. We worked closely with architects, engineers and owner [Taranaki entrepreneur Philip Brown] to budget the building in the very early stages, post tender.”
Foster Construction’s planned budget savings brought redesign of the conference area from a build-ability and cost point of view – simplifying the lobby, front entrance and staircase (the major items) – areas they thought could be pruned and made simpler.
“But the hotel has lost none of its style and star rating appeal,” Hope says.
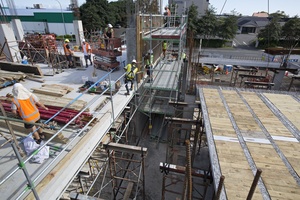
The 6000m2 site extends along an old gully that had previously been filled. There are few lay down areas for construction purposes and, with roads on two sides, businesses at each end and residential properties at the rear, management of noise and access is critical. SH3 Leach Street being a one-way system adds an extra factor to the management of the site.
“You have to do a lot of methodology, plan and review, days if not weeks ahead,” Hope says. We have quite stringent noise and environment controls to adhere to through the RM act, restricted hours of work and a tight deadline to meet; no noise before 10am Saturday and no work at all on Sundays. Add egress issues to the site makeup and it’s a very demanding site. The council has been great to work with.”
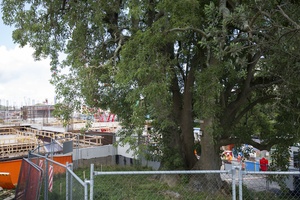
A church and two houses were removed from the site but an exotic, 150-year-old ombú tree remains, protected by resource management and contractual agreement. The tree, which grew in a plant nursery in the 1860s, is tall with a wide spread. It hails from South America and is thought to be one of two in New Zealand. Hope says Fosters has been commended on the care of the tree which was security ring fenced early in construction. Work around the tree is done by hand where possible to avoid damaging the roots and a local arborist makes regular visits to check on its health. The tree will be lit at night and will make a splendid natural and visual effect, Hope says.
“The client’s brief was that the tree must stay and the designers and builder are committed to this. It’s a win-win for everyone. This beautiful tree should command respect for many years to come.”
Below ground, geotechnical surveys had shown the gully, where a stream ended and rubbish had been dumped, would require work.
“Some design changes had to be made with the structural engineer due to unforeseen circumstances in the ground,” Hope says. There were areas of bad ground near the Leach Street frontage and better areas to the back of the property. We found spots of earth that had to be removed, and some were very deep.”
Once the land was reconstituted piled foundations were installed using driven steel ‘H’ piles.
“Local contractors Whitaker Civil completed those elements as well as the ground beams and column pads and the build is now into columns, precast beams and floor-pour stage.”
Structurally it is heavy construction with columns, beams and pre-cast tilt panels around the exterior and basement, Hope says.
“The beams, columns, floor ribs and in fills are fairly standard heavy construction, but it’s technically quite demanding to build with the way the column tops and beams interact with the overlay of stirrups. Add welding to many of the beam-to-floor stirrups and the building is up there in terms of design.”
Recent earthquake events and considerations for public safety have been strong motivators in structural design. The hotel has been divided into two separate buildings. A seismic break separates the three-storey west wing from the two-storey east wing, says Frank Kerslake, TSE structural and civil engineers. The suspended floors are a pre-stressed concrete rib system supported on concrete frames longitudinally. Transversally, concrete shear walls provide lateral support. A membrane roof on a timber truss roof system is suspended off a grid of structural steel beams.
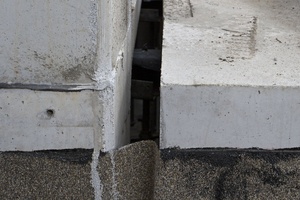
“Crane access to the hotel was assisted by the site layout. Vehicle access around three sides allowed mobile cranes to operate from multiple locations. The protected historical tree at the eastern end of the site did require special consideration during the planning, design and construction stages.”
Hope says the 100mm seismic break at grid line 11 makes the building compliant with the new regulations and allows it to give and hold as needed.
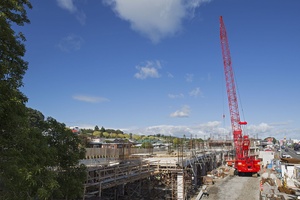
“The four concrete shear walls are for bracing. The staircase, and the main lifts A and B from the lobby back onto the shear wall on grid 12 and 25 (there are three lifts altogether). The building is the length of a football field with a curve so survey checking is a key.”
Porter Cranes from Hamilton trucked in “Big Red,” a 100-ton crawler crane to lift heavy beams and lighter tilt panels. The crane will be on site for six months.
“The good thing about a crawler crane is that you can physically pick up a load and, if you have to, you can move with that load. Other crane types are fixed in one position or on tracks.”
This is Foster Construction’s first contract in New Plymouth. The Hamilton-based company is building relationships, sourcing labour and materials locally as much as possible. They are partnering with ICL Construction for the pre cast, in-situ concrete and carpentry elements of the build. But Hope says construction in Christchurch and Auckland has placed pressure on both human and material resources.
“Our main test has been manpower and materials’ supply – getting things on site, on time and correct. There are good workers here but the challenge is mainly the numbers available to build a large building at the speed that’s required. Because of demand we have gone to labour hire places like Tradestaff and Onsite recruitment and brought in staff to do specific jobs.”
Nevertheless, come September, the hotel will be ready to open its doors and welcome its first guests.