Public Trust well placed
The Public Trust building, one of Wellington’s most ornate heritage treasures, has acquired a new lease of life – following damage sustained in the 2013 Seddon earthquake – as well as two highly suitable tenants: the Ministry of Culture and Heritage and a Jamie Oliver Italian restaurant.
Maurice Clark, a developer, engineer and the owner of the project’s main contractor, McKee-Fehl, bought the former Public Trust Office building in 2014 – an act considered by some as nothing short of heroic. Finding solutions for a fragile, 108-year-old building called for dedication, skill and a flexible budget.
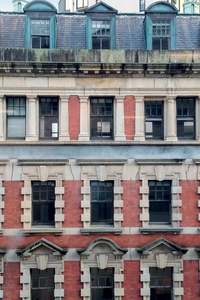
Designed by government architect John Campbell and completed in 1908, the Edwardian Baroque building needed to be strengthened and repaired. Clark brought in architects Warren and Mahoney, structural engineers Dunning Thornton and review engineers Beca, to upgrade the building to exacting modern standards, while maintaining the heritage values.
As both owner and contractor, Clark was in a unique position. Working to a cost-plus contract, the project team was able to alter designs and develop methodologies to suit the building, tenant needs, and heritage elements without the constraints of a fixed price.
“The combination of being a developer, an engineer and a contractor gives me certain advantages,” Clark says.
“This particular building proved to be considerably harder and more expensive than originally envisaged by the engineers and myself. I wanted to strengthen it to 90 per cent of code for the government tenants. The engineer was reluctant to do it to 100 per cent – [their position] for any older buildings. The engineering methodology, which engineers don’t always appreciate, is very much to do with tenant use and the final product, and also the heritage look. When you decide on a method of strengthening an old building you have to bear all those factors in mind. You have to balance a number of things all through the process.”
Three seismic strengthening methodologies were used: two pairs of shear walls across the width of the building at each end with energy-absorbing buckling beams between the pairs of walls at every level; a large diaphragm slab with post-stressing cable work; and steel rod reinforcing through the brick walls.
“It was quite a complicated methodology. The building is five storeys high so the G forces on the brick and stonework that might be 0.6 in the ground would be 3.5 when you get to the top, and this building has some very fancy stonework at the top,” Clark says.
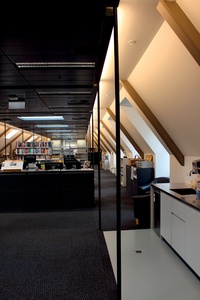
The original building structure was solid; it was based on a concrete-encased riveted steel I-beam frame – the first instance of a steel frame used for a building in New Zealand. In 1904, following an earthquake in San Francisco, the New Zealand Government had paid £1400 to Reid Brothers North American architectural practice for their expert advice on the design and construction of the frame; however, it was not up to modern-day design loads and codes.
Clark says the shear walls at each end allowed the 30m-long floor plate to remain unbroken. This, along with the five-and-half-metre height of the room, coupled with the restored ornate ceilings, will ensure the ground floor will make a wonderful space for the Jamie Oliver restaurant.
The shear wall and buckling beam method was chosen partly for its low visual impact and because it takes up less space when compared with a method such as buckling restrained braces (BRB). BRBs can’t take such concentrated loads and would be more visible as they tend to be positioned along building perimeters in the windows.
“In an earthquake the beams take the stress and buckle, so afterwards you cut them out and weld new ones in,” Clark says.
The substantial shear walls are Shotcrete and up to 450mm thick at some of the lower points.
“They are trowelled and left bare,” says architect Ralph Roberts of Warren and Mahoney. “We suggested that as they are new components to the building we don’t dress them and make them look heritage because they will become confused. The idea is that you showcase [the shear walls] as new and don’t necessarily bury them into the existing fabric of the building.”
The shear walls are connected to ground beams and fixed to the bedrock by a number of 20m-plus anchors.
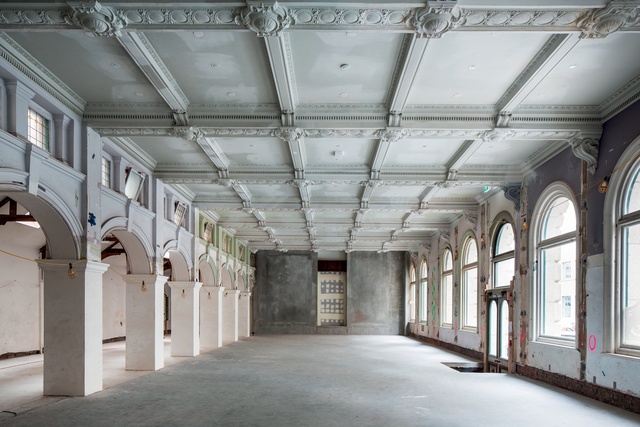
“The floors of the old building were not strong – they were steel framed with cinder concrete infill and a matai timber overlay. A new concrete floor was poured and strengthened with tendons – eight tonnes of pressure on each tendon to pull the building together between the shear walls,” Roberts says.
The decision to lift the 100-year-old matai floorboards was regretfully made but was necessary because the tenants didn’t want noisy wooden floors for their offices. Following a survey, cracks in the exterior of the building underwent minor repairs, as did corbels, cornices, dentils and other decorative features. However, damage to the heritage features was superficial and caused mainly by time, weather and pollution.
The exterior detailing is made of Tonga Bay granite from the Abel Tasman National Park. “It was used on a number of buildings but wasn’t of good quality,” Roberts says. “It had never crystallised properly during its geological formation; so, while the building has held its shape much of the detail on the surface is eroding. It has been cleaned and resealed, mortared where needed and in some places, as part of the strengthening, the bricks have been saw cut to allow them to move and be more flexible in an earthquake. The tensioning holds the bricks and other building materials together.”
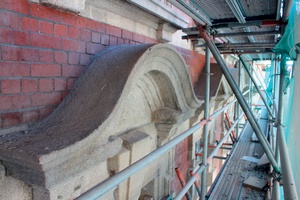
The building’s top-to-bottom makeover also included cleaning the copper dome and repairing the Welsh slate roof, re-installing a flagpole and repainting the timber dormer window frames. The interior shell of the building was refurbished for modern usage – new sprinklers put in, new wiring, transformers, switchgear, and the old lift was replaced. “The lift shaft was like a corkscrew so we had to straighten all that up,” Clark says.
New dark-metal panned ceilings float above the open-plan office spaces on floors one to four, reducing the height of the workspace while retaining the integrity of the building. The basement area that was once a car park is being converted into a beer cellar and will also provide kitchen storage and back-of-house amenity for the restaurant.
A new staircase that connects all the floors was installed with a simple timber and brass handrail and lit with LED lights. The original had been removed and replaced in the 1980s as it was non-compliant. “But you don’t try and rebuild an old kauri stair, which is what there was originally,” Clark says. “So the architects designed a very minimalistic modern stair that sits lightly within the high ceilings and within the more ornate fabric and style of the building.”
They applied the same transparent approach to the groundfloor rotunda and staircase. Where tiles have been damaged and removed, rather than copying them they have plastered the patches where the tiles were and painted the space, acknowledging they can’t be replicated and avoiding confusion between old and new.
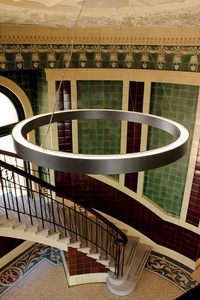
Finding locations for a modern plant in this relatively small (1300m2) heritage building called for lateral thinking and a reuse of existing space. “The challenge for old buildings is to not disrupt the architectural quality of the building and to find new spaces/parts of the building to locate modern kit,” Roberts says.
The chiller, handling plant (for a bespoke, fan-coil air-conditioning system, suitable for Wellington’s marine environment) and the main switchboard were “carefully fitted” into the space above the old vehicle dock bay towards the north end of Stout Street. “The old motors on top of the lift shaft were removed, and as the new lift systems are more compact the residual space could be used for mechanical services,” Roberts says.
Other tricky tasks included removing asbestos under the floors and sandy soft fill under the basement slab, which they vacuumed out, then re-injected the spaces with concrete fill. Drilling the piles was another challenge that required cutting out the basement and working in a confined space.
“Cost plus was the only way to do it; you couldn’t give a fixed price. You have to react to things as you find them,” Clark says. The final cost of the project was $10 million and while the budget blow-out may not impress Clark, he is very pleased with the result. “I’ve been amazed at the response from people saying how much they love the building.”
And at night the building’s façade adds character to the streetscape with its features illuminated by small LED lights, in a scheme designed by ECC. The new government tenants are now happily ensconced and Jamie Oliver’s restaurant is expected to open at the end of this year.