The high cost of corrosion
The damage bill from corrosion is estimated at $9 billion annually. Progressive Building looks at one type of corrosion, concrete, and how the industry is working together to combat its steady march.
Given the financial toll, not to mention the downtime needed to remediate the effects of corrosion, it’s no wonder the industry continues to throw its weight behind research and development designed to mitigate, if not eradicate, this pervasive problem.
Most of us would be familiar with the most common sign of corrosion – rust. However, few might know that rust has a much higher volume than the originating mass of iron or steel it is corroding. Consequently, its build-up can cause failure by forcing apart adjacent parts – a phenomenon referred to as ‘rust packing’.
Rust packing is known to have caused the collapse of a 30m section of the Mianus Bridge in Greenwich, Connecticut, on 28 June 1983. The collapse was caused by the failure of two pin and hanger assemblies that held the deck in place on the outer side of the bridge. Rust formed within the bearing of the pin, exerting a force on the hanger, which was beyond design limits for the retaining clamps. It forced the hanger on the inside part of the expansion joint at the south-east corner off the end of the pin that was holding it, and the load was shifted to the outside hanger.
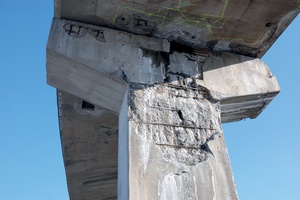
The extra load on the remaining hanger started a fatigue crack at a sharp corner on the pin. When it failed catastrophically, the deck was only supported at three corners. When two heavy trucks and a car entered the weakened section at 1:30am, the remaining expansion joint failed and the deck crashed into the river 21m below. Three people were killed in the incident and a further three injured.
When the affected iron or steel is situated within concrete, the expansive force created by the rust’s additional volume causes the concrete to spall, in turn triggering severe structural problems including collapse.
“How do we learn from corrosive failures, so that the concrete industry can employ better techniques in the future?” asked Stewart Hobbs of proConsult Limited, at the recent Australasian Corrosion Association Roadshow.
Because concrete has high compression strength but comparatively weak tension, it usually needs steel rebar to reinforce the structure’s tensile strength. When first installed, a concrete paste protects the steel bars from carbonation and chlorides within the concrete, but over time this protection is lost and the steel will start to corrode. As we understand more about the behaviours of various concrete compositions, and poor welds in relation to each other and to other materials, we’re able to start designing concrete-based structures more effectively.
Corrosion can be caused by a number of factors, such as:
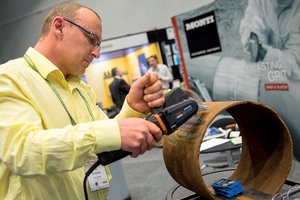
- A structure not being completely watertight, which can also be caused by poor detailing
- Its proximity to the sea or sea spray, which most New Zealand buildings are considered to be – especially in the major cities
- Inadequate corrosion protection for the life of the building. A cost analysis will need to be done to determine the correct levels for this
- A poor maintenance programme, including appropriate protective coating systems.
Engineers concede that corrosion can never be completely eliminated, but deterioration can be slowed and a good maintenance plan will help.
Concrete breaks down over time due to a number of factors including chlorides, carbonation, alkali-silica reaction, sulphate attack, shrinking or thermal cracking, soft/hard water, and attacks from other chemicals. By the time corrosion can be seen by the naked eye, it’s already well advanced and remediation options need to be considered. These can include: chloride extraction; re-alkalisation; protective coatings or tape wraps depending on the structure; crystalline surface treatments; patch repairs such as sacrificial anodes (to prevent incipient anodes forming); and cathodic protection.
Patch repairs are the most popular method for repair in New Zealand says GHD’s Sean Ryder, NZ Material Technology Group Coordinator, a speaker at the roadshow. It’s a relatively cheap process that removes contaminated concrete at the concrete corrosion’s location (not the source), and is a good solution for small areas.
However, Ryder warns that a patch typically has only a five to ten-year service life, is labour intensive to complete and that unless precautions are taken, the process can create incipient anodes which simply move the problem elsewhere within the structure.
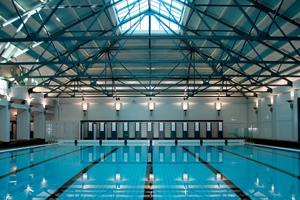
Chloride extraction and re-alkalisation are also relatively inexpensive but, according to Ryder, there are few contractors in New Zealand experienced in these procedures. Both methods require an appropriate protective coating following treatment to ensure either chlorides or carbonation don’t re-enter the concrete.
Using protective coatings alone cannot remove contaminants that have already entered the concrete and in fact the coatings may trap them in there. However, if concrete is coated when the asset is installed or commissioned, it can prevent contaminants from entering the concrete for a time. Coatings can include special paints as well as wraps depending on the asset’s location.
Crystalline technology slows corrosion by migrating into the concrete and blocking pores to prevent contaminants and moisture from entering. No maintenance is required for this process, and in some cases it may be able to bind contaminants if they are already present, “especially if they’re not near any rebar,” says Ryder. Its performance is dependent on the concrete characteristics at the individual site.
He believes that cathodic protection is the only proven method of preventing further corrosion once it has already begun. It’s a relatively expensive process that works by turning a metal surface into the cathode of an electro-chemical cell. For concrete, introducing a DC electrical current to rebar will therefore prevent it corroding, or corroding further.
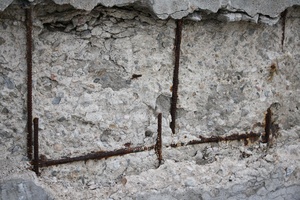
There are now a number of non-destructive ways to determine whether corrosion is present before it’s visible on the surface. Richard Nowak of Olympus outlined ultrasonic and videoscope inspection options available to asset owners.
“Ultrasonic measurement uses echo-sounding techniques similar to sonar, to measure any changes in thickness of a material. The velocity of these waves is fixed by the thickness and type of material being tested,” he explains. The device sits on the external surface of the area, and pulses from a transducer are shown on a screen. “For corrosion applications, twin-crystal transducers give the most accurate results,” he says.
A phased array scanner is often used to check large areas quickly. Resulting data can then be logged and transferred to a spreadsheet or database. Such devices are becoming faster and more economical, and offer comprehensive mapping options of an area, with better sensitivity than had previously been available.
If images are needed from inside the structure, Nowak suggests a videoscope be used. This device records either stills or videos and includes a thin, flexible probe at the end of which is a tiny camera with its own light source. Lenses can be interchangeable to offer everything from a 40-degree field of view up to 120 degrees, with ‘near’ or ‘far’ focus options and direct or side viewing. They are often used to verify the presence of corrosion following NDT testing and to access high, low or otherwise difficult-to-reach areas. “This method offers visual confirmation of corrosion if necessary,” he says.